Can science save the oil sands?
NATHAN VANDERKLIPPE
Globe and Mail
April 24, 2009
Falling oil prices and bad PR have hammered the oil sands. Out of all that bad news may rise a new era in innovation
FORT McMURRAY, ALTA. — If Selma Guigard is right, an elusive key to reducing the oil sands' emissions could lie in the science of the super-critical molecule.
When they are subjected to a certain high temperature and pressure, substances like carbon dioxide enter a state where they are neither liquid nor gas — the super-critical state. When mixed with several other compounds, super-critical carbon dioxide is able to extract hydrocarbons from almost anything, in a process somewhat like the way some dry cleaners work.
Dr. Guigard, an associate professor of environmental engineering at the University of Alberta, is trying to prove it can do the same for the Athabasca oil sands. This is not a mere science experiment: Lab modelling has shown that her process uses virtually no water, and less than a third of the energy spent today on bitumen extraction.
That makes it not only a potentially huge step up from an environmental point of view, it could also help redraw the economics of the oil sands.
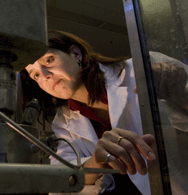 Dr. Selma Guigard, an engineering professor at the University of Alberta, has developed a method for extracting bitumen from the oil sands that uses almost no water and far less energy. (John Ulan/For The Globe and Mail) |
There's only one problem. To prove the technology, Dr. Guigard needs to build a small pilot operation, and that will cost $1-million. She's spent a year banging on the doors of the energy companies that stand to gain the most from what she is developing.
They have all declined.
"The response is basically they're looking at this as still in its infancy, and so they are waiting for a little bit more research," she said.
That puts Dr. Guigard in a bind: "They want us to be further along than we can get with the funding sources that we currently have."
Talk to anyone in Calgary or Fort McMurray, and they will tell you that the story of the oil sands has been the story of technology. Were it not for the original hot-water extraction method, mining would never have become profitable decades ago. Were it not for the next step, the steam-assisted gravity drainage (SAGD) techniques developed in the 1970s that use high-pressure steam to send bitumen dripping out, the more-expansive deeper oil sands would never have been tapped.
But those are by and large yesterday's techniques and methodologies. In the past nine months, the dive in oil prices has brought more than $200-billion in spending plans crashing off books, raising profound questions about the ability of the industry to prosper in the future.
In large measure, $50 (U.S.) oil has put existing oil sands technologies on life support. In recent years, companies spent half as much of their revenue on research and development as the rest of industrial Canada — far less than even farmers and fishermen.
The lack of research has helped contribute to the vulnerability of the industry to falling oil prices. Last summer, a company building a new oil sands mine needed $90 oil to be profitable. Anyone building a new SAGD operation needed $70 oil.
Costs have begun to dip in the cooling of the boom. But if ever there was a time for someone to come up with a new way of producing the oil sands — a way that's both cheaper and less environmentally heavy footed — it's now.
Several companies are chasing ways to do exactly that, using electric currents, underground fires and petrochemical solvent cocktails to accomplish leaps in efficiency and lower greenhouse gas emissions. Many of the boldest ideas, however, belong to the oil patch outsiders. They are the upstarts — the mavericks — seeking to claim Fort McMurray's future with a new vision of how oil can flow.
But that new vision is unlikely to transform the oil sands if left to the small companies alone. Both government and industry heavyweights have been slower to embrace the need for new technology.
If they do not adapt to the future and start to invest more heavily, Canada's energy industry risks shrivelling, said Jamie Blair, a former Husky Canada executive who is now advocating for a new technological era in Alberta.
"People will talk about the oil sands being on the backburner," he said.
NEW TECHNOLOGIES
Ever since oil began its long dive last summer, a torrent of callers has been ringing Bruce McGee's phone. Every time he answers, he tells investors, energy companies and whoever else who will listen this story: He believes his company, E-T Energy Ltd., can produce oil at a profit with prices at $26 a barrel.
Mr. McGee, who is president, believes that changes everything. By his calculation, E-T's technology can be used to pump out 600 billion barrels of oil sands bitumen. That's more than triple the Alberta government's best guess at what's currently recoverable from the oil sands, and enough to satisfy total global demand for two years.
"Once we get out there and we're putting barrels on the balance sheet, we're going to have more barrels on our balance sheet than Saudi Arabia in a very short period of time," says Mr. McGee, the company's president. "We won't be second. We will be first in the world."
It could also tear apart current oil sands practices.
"If the price of oil stays at $40 a barrel, it will replace mining," predicts Craig McDonald, E-T's vice-president of operations. In coming weeks, the company will hit the road to raise $150-million to commercialize its technology.
That technology isn't much to look at — just a few well heads and large tanks sitting on a windswept field south of Fort McMurray. A series of electrodes dangle in each well. When they are turned on, they pass a current through the earth — like electricity through a stove element — and heat it up. The result: The bitumen, which is normally locked in sand as hard as rock, begins to flow — like molasses in a microwave. No huge mines needed, no greenhouse gas-spewing steam projects required.
In a place accustomed to prying bitumen from the earth using monstrous shovels and vast quantities of steam, this pilot project is a bold attempt to reshape the environmental and financial costs of the oil sands.
In other parts of Alberta, companies are using radically different techniques: Petrobank Energy and Resources Ltd. is studying how to free bitumen using underground combustion, while Laricina Energy Ltd. is mixing steam with solvents, which dramatically cuts the amount of natural gas used to extract bitumen from deeper oil sands. At universities and provincial research bodies, scientists are studying how microbes could be used in bitumen upgrading, and examining the effectiveness of new techniques inside specially modified medical CT scanners.
All of the major oil sands players maintain research divisions that pour millions of dollars into perfecting extraction processes every year. Some, like ConocoPhillips and Syncrude, are holding those budgets steady in the current downturn (Syncrude alone spends $50-million a year), while Shell has said its R&D budget will drop this year.
Others, like Imperial Oil, are ramping up: The company spent $117-million on research last year, more than double its 2006 budget. It has established a centre for oil sands innovation at the University of Alberta, and plans to build a pilot to test its own version of the solvent technology this summer.
Imperial, like many other companies, maintains that research is a crucial to its future. "Our greatest lever for profitability is technology development," said Imperial spokesman Pius Rolheiser.
R&D LAGS
Indeed, between 2004 and 2006, the most recent year Statscan has numbers, the entire industry's research spending grew by 65 per cent to $515-million.
But compared to other industries, and to their own outsized earnings, energy companies are well behind on research spending. Imperial Oil alone pulled in $3.9-billion in profit last year.
Statistics Canada's most recent figures on R&D spending as a percentage of revenue, from 2006, show the national average among all industries is 2 per cent. Pharmaceutical companies spent 6.7 per cent; the agriculture industry 1.6 per cent; forestry and logging 4.4 per cent; fishing, hunting and trapping 5.8 per cent. Oil and gas companies spent 0.9 per cent.
And not all of the spending is going toward finding new extraction methods. Substantial sums are being spent on improving tailings technology and perfecting extraction processes currently in place.
Those who have experience in the oil sands charge that the companies that work there are not open enough to new thinking.
"They've gotten so complacent and so fixed in the way they've done business up there," said Paul Verhesen, the president of construction firm Clark Builders, which has done work in the oil sands. "They'll spend $1,000 to save $1 as opposed to being innovative, being creative, being willing to look at options."
For many years, there was little incentive to spend on research. Rising oil prices made existing technologies abundantly profitable, masking a need for change. Instead of searching out better extraction technology, energy companies focused more attention on geological innovation: Finding better ways to discover and measure how much petroleum is beneath the surface.
And compared with industries like biotechnology, which spend heavily to grow and develop, the energy industry is mature, "so they don't spend as much" on technology, said Peter Tertzakian, the chief energy economist for Calgary-based ARC Financial.
What's needed, he said, is for the industry to undergo a "renaissance" that requires a boost in spending.
Part of the responsibility also lies with government, which has, in the past, been integral to pushing the oil sands forward. The Alberta Oil Sands Technology and Research Authority, or AOSTRA, was created by the Alberta government in 1974 to help lower the cost of oil sands development. It succeeded in laying the foundations for the SAGD technology that is in use today.
The Alberta and Saskatchewan governments are both spending money on provincial research bodies that are looking for new solutions. Most notably, Alberta is spending $2-billion over the next 12 years to help develop carbon capture and storage technology.
But less is being spent on the extraction technologies that are most critical to oil sands economics and environmental footprint. In its heyday in the mid-1980s, AOSTRA received more than $70-million in annual funding. Its best current counterpart, the Alberta Energy Research Institute, received $44-million last year, and its executive director, Eddy Isaacs, said the problems that need solving today — cost concerns intermingled with environmental and greenhouse gas issues — are far more complex. Mr. Isaacs said his budget needs to be more than doubled, "at the very least."
There is, however, growing hope that Alberta's sudden decline in fortunes has brought an appetite for change rushing back to the oil patch. And it is coming in expected places.
A NEW SURGE OF INNOVATION?
Take Jamie Blair, for example, a man whose pedigree easily ranks among the best in Alberta. Mr. Blair served as chief operations officer for one of Calgary's biggest conventional oil firms, Husky Oil. His father, the late Bob Blair, founded and led Nova Corp., the Alberta icon that almost single-handedly built a petrochemicals industry in the province. His grandfather, Sid Blair, helped develop the pioneering hot-water extraction process in the 1920s, a critical development that used hot water to lift bitumen from mined oil sands and opened the way for the first Athabasca oil sands mine decades later.
Mr. Blair still has a copy of the thesis statement on that process that his grandfather co-authored. What bothers him is that it's not a historical document: Hot-water separation remains an integral part of modern oil sands mines, many decades after it was first commercialized.
Advances in recent years have helped cut in half the temperature at which the process is done — lowering its energy requirements — but "the work that [Sid Blair] was doing in a lab up at the University of Alberta a million years ago is still the technology of today," he said. "And the upgrading technologies, again, haven't made leaps forward."
Mr. Blair himself is helping fund some research at the University of Calgary that is experimenting with microbes in hopes of making "quantum" savings in the energy required to process bitumen.
But he accuses industry of being afflicted with a "syndrome of 'you can't change the technology.'" He points to the business of natural gas as an example of what's possible. In the past decade, that industry has found itself suddenly able to tap enormous new bodies of natural gas after the development of new drilling and rock-fracturing technologies enabled it to access shale gas, which had previously been considered uneconomic.
The results have been dramatic. In one shale alone, the Barnett in Texas, the U.S. Geological Survey estimated technically recoverable reserves of three trillion cubic feet in 1996. By 2008, the best estimate was 55 trillion cubic feet — a stunning 18-fold increase in what could be economically extracted from one area, thanks almost entirely to technological advance.
The oil sands is in dire need of such a makeover, Mr. Blair said — but has been hampered from trying to change by the past decade's steady surge in crude prices.
"We've seen oil price increases make the old technology seem very practical," he said. "But particularly in today's environment, where oil prices have now retreated dramatically and the challenge is now on cost and efficiency, it puts a harder perspective on things."
"And are people going to rise to the challenge? Yes."
They have in the past, and there are examples where they are today. In 1982, Imperial Oil patented the revolutionary steam-assisted gravity drainage technology now used in most new projects. The result: Industry suddenly gained access to a huge new resource of deep bitumen deposits, all without using the gaping open-pit mines that have drawn such environmental ire.
More recently, Shell has experimented with electrical extraction — using a different method from E-T — and produced 100,000 barrels of oil at a test site near Peace River, although that technology is not yet commercially ready.
Yet early stage efforts remain a bet fraught with risks.
E-T has stumbled in its attempts to apply the technology to the oil sands (it has worked dozens of times in environmental remediation applications). In its second major test, it managed to produce oil from only one of four wells. Its problems ranged from electrical cables that were accidentally severed by surface equipment, to the design of its electrodes. In total, E-T has produced less than 3,000 barrels of oil.
Yet the potential prize for success is huge. E-T's technology, for example, could help open up carbonate oil, a huge hydrocarbon resource that is so tricky to produce that virtually no one has tried. And Petrobank believes its process, which uses a controlled underground burn to intensely heat oil sands and make them flow, can be used in a huge variety of heavy oil fields around the world. Like E-T's process, it requires virtually no water and uses dramatically less energy.
"We are breaking new ground in the industry," said Chris Bloomer, Petrobank's chief operating officer for heavy oil.
He knows doubters think it won't work. He remembers when skeptics said steam-based extraction wouldn't work, either. They believed gravity would have no force in the reservoir, and the oil simply would not flow out. They were wrong then, and he believes they're wrong now.
Will the rest of the industry agree?
Mr. Blair is optimistic that low oil prices are cracking old resistance to change. The way he sees it, companies have two choices: Wait for oil prices to jump high enough that oil sands projects are economic again, or "get there first by being the first on the block to implement newer and more efficient technology."
"It seems like an easy choice to me," he said. "But it takes leadership. It takes innovators."
Posted by Arthur Caldicott on 25 Apr 2009
|